OUR HIGH-QUALITY ALLOYS CASTING
High-quality alloys in refiner discs are essential for several reasons, impacting the efficiency, durability, and performance of the refining process. Here's why good alloys are important:
1. Wear Resistance
Longevity: High-quality alloys offer superior wear resistance, which is crucial in the harsh refining environment where discs face continuous abrasion from wood chips and mechanical stresses.
Reduced Downtime: Longer-lasting discs lead to fewer replacements and maintenance, minimizing production downtime and associated costs.
2. Performance Efficiency
Stable Performance: Alloys that maintain their properties under high temperatures and pressures ensure consistent refining performance, resulting in uniform pulp quality.
Energy Efficiency: Good alloys can reduce energy consumption by maintaining effective cutting and shearing actions over time, leading to cost savings in energy.
3. Mechanical Strength
Durability: High-strength alloys can withstand the mechanical forces applied during refining without deforming or failing, which is essential for maintaining optimal operational conditions.
Operational Safety: Strong alloys reduce the risk of disc failures, which could potentially cause accidents or damage to the refining equipment.
4. Temperature Tolerance
Heat Resistance: During refining, significant frictional heat is generated. Alloys with high-temperature tolerance maintain their hardness and performance, ensuring the refining process is not compromised by thermal effects.
5. Surface Integrity
Precision: Good alloys help maintain the integrity of the disc’s bar patterns and grooves, which are critical for the effective separation and development of fibers. This precision directly influences the quality of the pulp produced.
6. Cost Efficiency
Overall Value: Although high-quality alloys may have a higher initial cost, their extended lifespan and improved performance often lead to better overall value by reducing frequent replacements and improving refining efficiency.
Using high-quality alloys in refiner discs is crucial for ensuring durability, efficiency, and consistency in the refining process. These alloys contribute to the overall effectiveness of pulp production, affecting both the quality of the final product and the operational costs..
ROLE OF USING REFINER DISC
The refiner disc's role and its bar pattern are fundamental in the mechanical refining process of wood chips to produce pulp for paper manufacturing.
Role of Refiner Discs
Fiber Separation: The primary role of the refiner disc is to separate and individualize the wood fibers. As wood chips pass between the rotating discs, the mechanical action helps break down the lignin bonds between fibers, leading to the liberation of individual fibers.
Fiber Development: Refining improves the physical properties of fibers, such as their length, flexibility, and surface area. This enhancement is crucial for the bonding strength and overall quality of the final paper product.
Pulp Consistency: Refiner discs help achieve a consistent pulp consistency by controlling the degree of refining. This ensures uniformity in the paper product, affecting its strength, density, and appearance.
Energy Efficiency: Effective refining with well-designed discs can optimize energy usage. Properly balanced discs reduce the amount of energy needed to achieve the desired fiber development, making the process more cost-effective.
Bar Pattern
The bar pattern on the refiner disc consists of various grooves, ridges, or teeth arranged in specific configurations. These patterns are designed to create shear and compressive forces on the wood chips, facilitating effective fiber separation.
· Impact on Pulp Quality : The choice of bar pattern affects the refining action. For instance, a disc with a high number of fine bars may produce more highly refined pulp, while a disc with fewer, coarser bars may be more suitable for initial fiber separation.
· Wear and Maintenance : The bar pattern also influences the wear and maintenance of the discs. Patterns that cause excessive wear might require more frequent replacements, while more durable patterns can extend the service life of the discs.
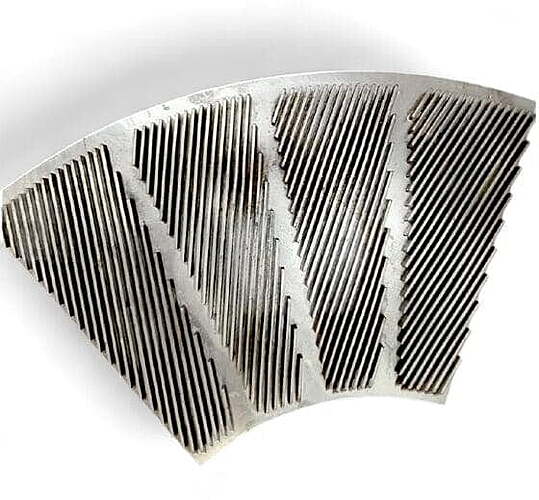